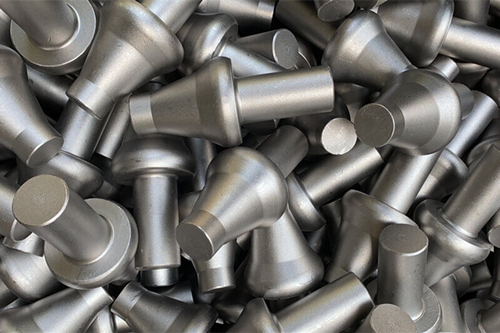
The Cold Forging Process – 5 Important Things Manufacturers Always Considers
On July 17, 2023 by rimrockCold forging is a highly efficient and widely used manufacturing process that involves shaping metal parts using compressive forces at room temperature. Manufacturers across various industries rely on cold forging to produce high-quality components with exceptional strength, precision, and cost-effectiveness.
However, to ensure successful cold forging operations, manufacturers must carefully consider several crucial factors. In this article, we will explore five important considerations that manufacturers always keep in mind during the cold forging process.
Material Selection
The choice of material is paramount in cold forging. Manufacturers must select metals with excellent cold formability, such as aluminum, copper, steel, and their alloys. These materials possess desirable characteristics like high ductility, low work hardening rates, and good flow properties when subjected to compressive forces. Material selection also depends on the intended application and the specific requirements of the final product, including strength, durability, and corrosion resistance.
Die Design and Preparation
The design and preparation of the forging dies play a vital role in achieving accurate and consistent cold forging results. The dies must be precisely engineered to impart the desired shape and dimensions to the workpiece. Factors such as die material, die lubrication, die clearance, and cavity design need to be carefully considered. The die geometry should be optimized for uniform material flow, minimize the risk of defects, and enhance the overall productivity of the process.
Machinery and Equipment
Choosing the right machinery and equipment is crucial for achieving optimal cold forging results. Manufacturers invest in high-quality presses, hammers, or specialized cold forging machines capable of exerting sufficient force to shape the metal. The equipment must provide precise control over the forging process, allowing adjustments in stroke length, forging speed, and dwell time. Additionally, advanced monitoring and automation systems are often employed to ensure consistent quality and productivity.
Quality Control and Testing
To maintain stringent quality standards, manufacturers implement comprehensive testing and inspection procedures throughout the cold forging process. Various non-destructive and destructive testing methods, including dimensional inspection, hardness testing, ultrasonic testing, and microstructure analysis, are employed to verify the integrity of the forged components. These quality control measures enable manufacturers to identify and rectify any defects or deviations promptly, ensuring that only parts meeting the required specifications reach the market.
Click here for the best cold forging manufacturers in the market.
Archives
Calendar
M | T | W | T | F | S | S |
---|---|---|---|---|---|---|
1 | 2 | |||||
3 | 4 | 5 | 6 | 7 | 8 | 9 |
10 | 11 | 12 | 13 | 14 | 15 | 16 |
17 | 18 | 19 | 20 | 21 | 22 | 23 |
24 | 25 | 26 | 27 | 28 | 29 | 30 |
31 |
Leave a Reply